Các phương pháp phủ chất quang dẫn thường được chia thành lớp phủ quay, lớp phủ nhúng và lớp phủ cuộn, trong đó lớp phủ quay được sử dụng phổ biến nhất. Bằng cách phủ quay, chất quang dẫn được nhỏ giọt trên bề mặt và chất nền có thể được quay ở tốc độ cao để thu được màng quang điện. Sau đó, có thể thu được màng rắn bằng cách đun nóng trên bếp điện. Lớp phủ quay thích hợp để phủ từ màng siêu mỏng (khoảng 20nm) đến màng dày khoảng 100um. Đặc điểm của nó là tính đồng nhất tốt, độ dày màng đồng đều giữa các tấm wafer, ít khuyết tật, v.v. và có thể thu được màng có hiệu suất phủ cao.
Quá trình phủ quay
Trong quá trình phủ quay, tốc độ quay chính của chất nền quyết định độ dày màng của chất quang dẫn. Mối quan hệ giữa tốc độ quay và độ dày màng như sau:
Quay=kTn
Trong công thức Spin là tốc độ quay; T là độ dày màng; k và n là các hằng số.
Các yếu tố ảnh hưởng đến quá trình phủ spin
Mặc dù độ dày màng được xác định bởi tốc độ quay chính, nhưng nó cũng liên quan đến nhiệt độ phòng, độ ẩm, độ nhớt của chất cản quang và loại chất cản quang. So sánh các loại đường cong lớp phủ quang điện khác nhau được thể hiện trong Hình 1.
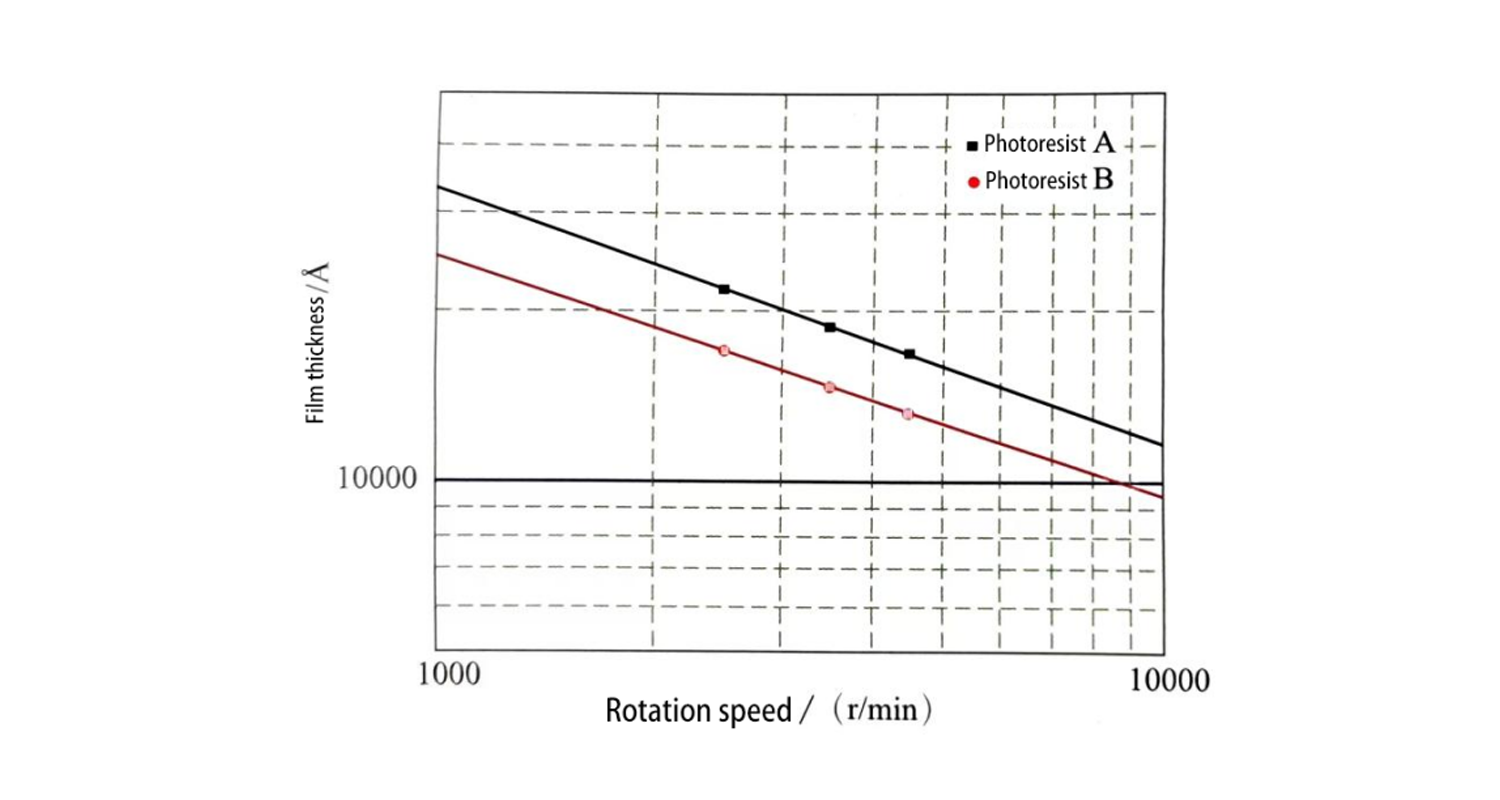
Hình 1: So sánh các loại đường cong lớp phủ quang điện khác nhau
Ảnh hưởng của thời gian quay chính
Thời gian quay chính càng ngắn thì độ dày màng càng dày. Khi thời gian quay chính tăng lên, màng càng mỏng. Khi vượt quá 20 tuổi, độ dày màng hầu như không thay đổi. Vì vậy, thời gian quay chính thường được chọn lớn hơn 20 giây. Mối quan hệ giữa thời gian quay chính và độ dày màng được thể hiện trong Hình 2.
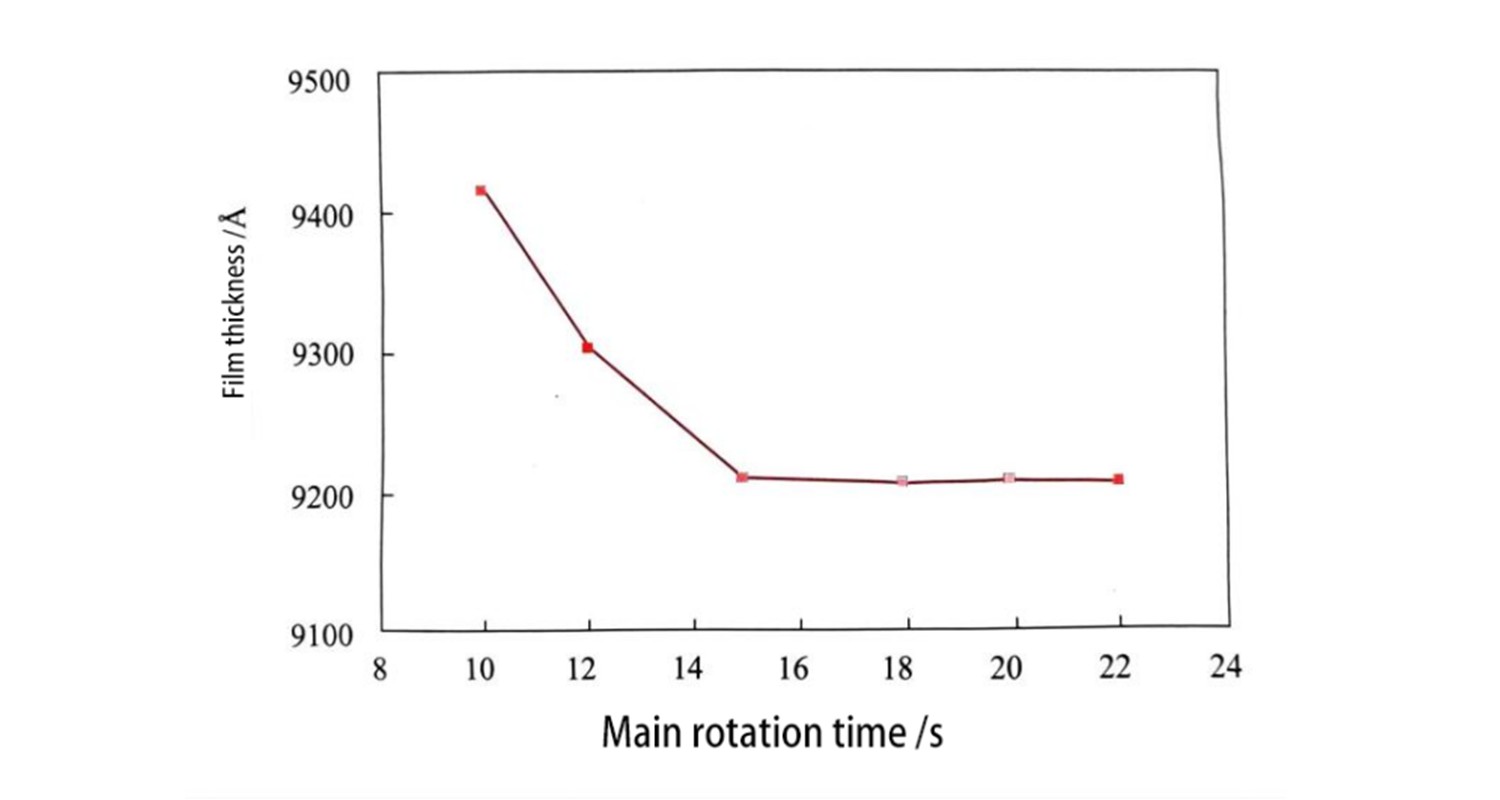
Hình 2: Mối quan hệ giữa thời gian quay chính và độ dày màng
Khi chất quang dẫn nhỏ giọt lên bề mặt, ngay cả khi tốc độ quay chính tiếp theo là như nhau, tốc độ quay của chất nền trong quá trình nhỏ giọt sẽ ảnh hưởng đến độ dày màng cuối cùng. Độ dày của màng chất quang dẫn tăng lên khi tốc độ quay của chất nền tăng lên trong quá trình nhỏ giọt, điều này là do ảnh hưởng của sự bay hơi dung môi khi chất quang dẫn được mở ra sau khi nhỏ giọt. Hình 3 cho thấy mối quan hệ giữa độ dày màng và tốc độ quay chính ở các tốc độ quay bề mặt khác nhau trong quá trình nhỏ giọt chất quang dẫn. Có thể thấy từ hình vẽ rằng khi tốc độ quay của chất nền nhỏ giọt tăng lên, độ dày màng thay đổi nhanh hơn và sự khác biệt rõ ràng hơn ở khu vực có tốc độ quay chính thấp hơn.
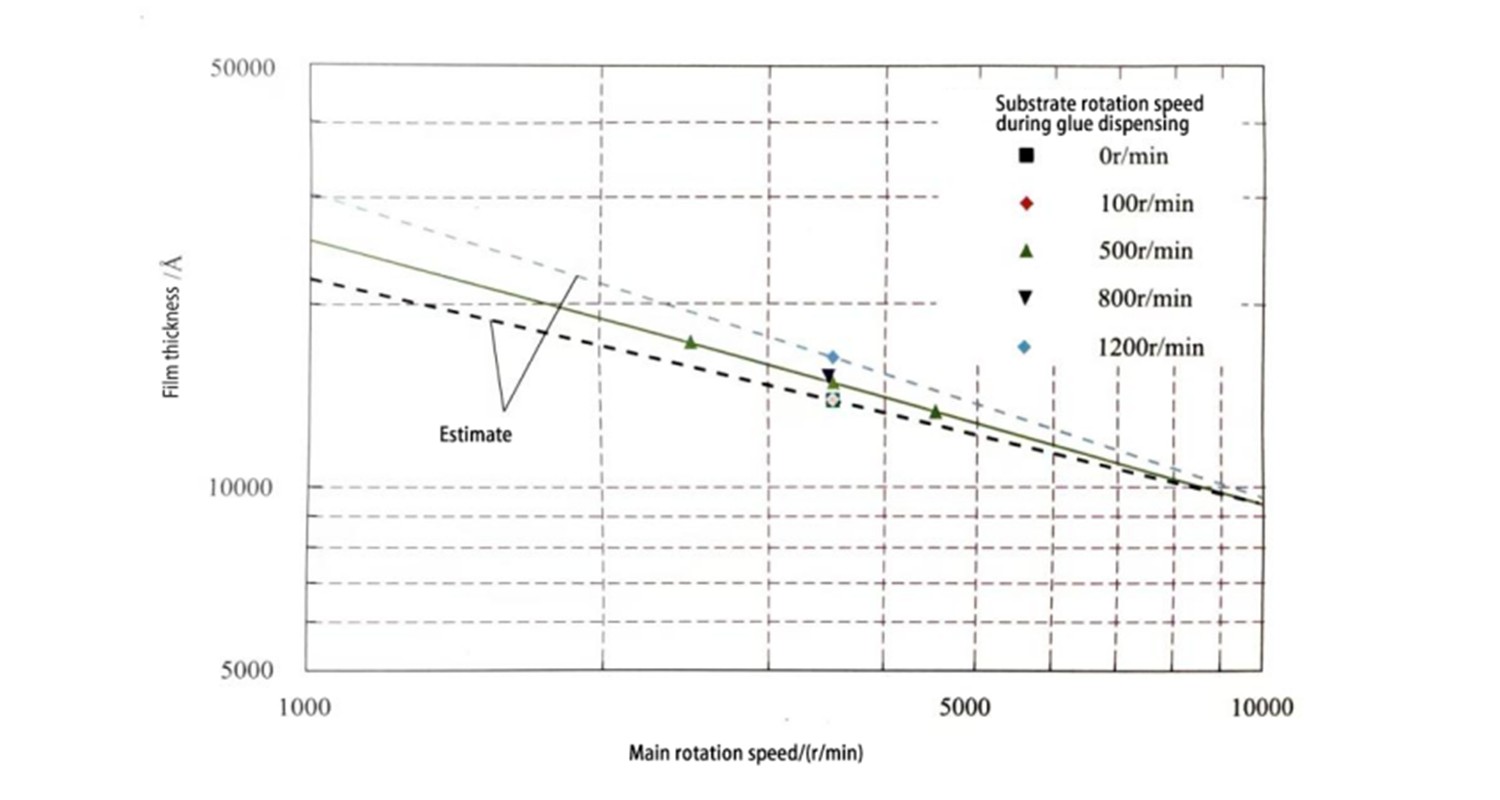
Hình 3: Mối quan hệ giữa độ dày màng và tốc độ quay chính ở các tốc độ quay bề mặt khác nhau trong quá trình phân phối chất quang dẫn
Ảnh hưởng của độ ẩm trong quá trình phủ
Khi độ ẩm giảm, độ dày màng tăng lên, do độ ẩm giảm sẽ thúc đẩy quá trình bay hơi của dung môi. Tuy nhiên, sự phân bố độ dày màng không thay đổi đáng kể. Hình 4 cho thấy mối quan hệ giữa độ ẩm và phân bố độ dày màng trong quá trình phủ.
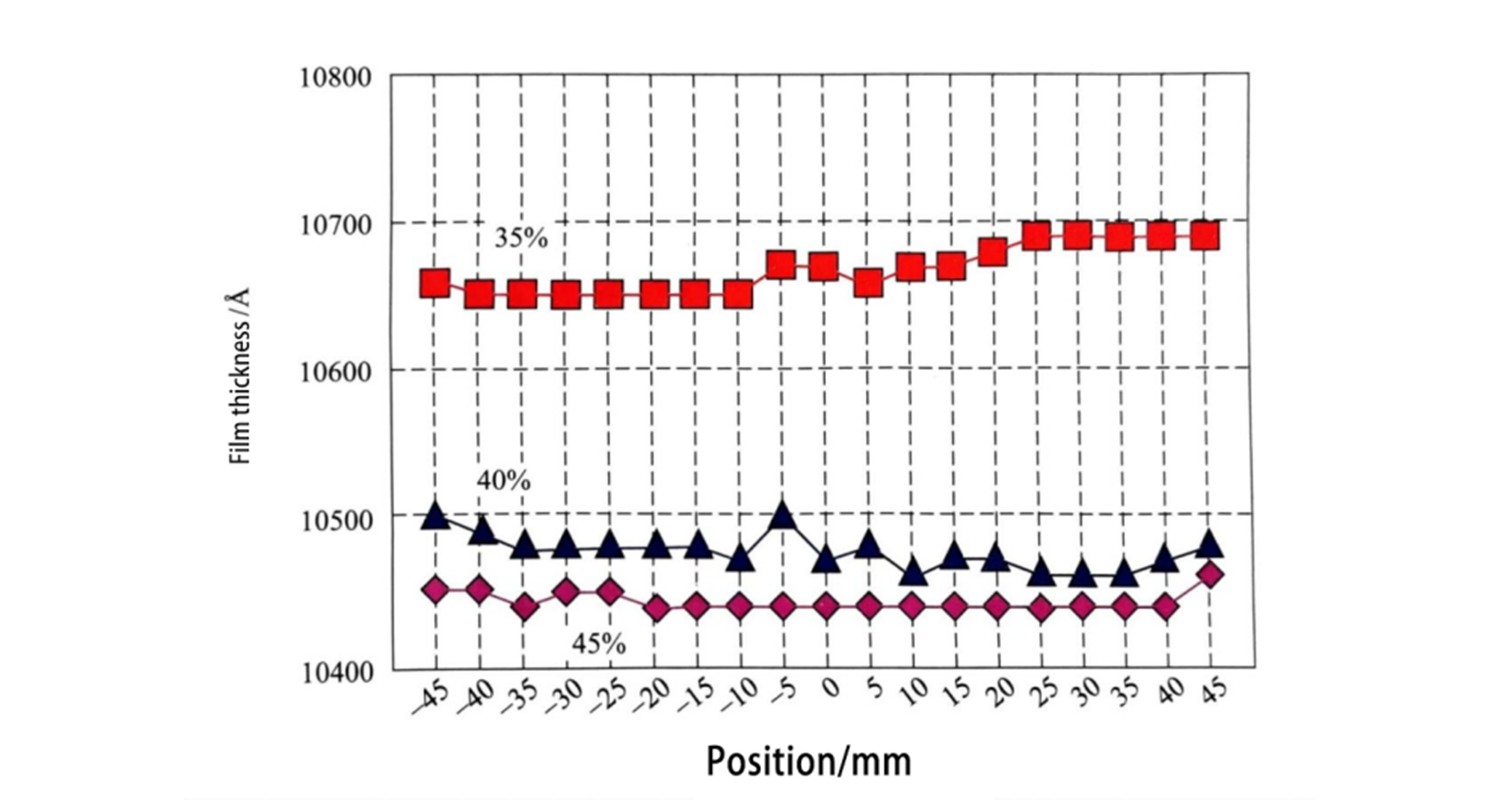
Hình 4: Mối quan hệ giữa độ ẩm và phân bổ độ dày màng sơn trong quá trình phủ
Ảnh hưởng của nhiệt độ trong quá trình phủ
Khi nhiệt độ trong nhà tăng lên, độ dày màng sơn tăng lên. Có thể thấy trong Hình 5 rằng sự phân bố độ dày màng quang điện thay đổi từ lồi sang lõm. Đường cong trên hình cũng cho thấy độ đồng đều cao nhất đạt được khi nhiệt độ trong nhà là 26°C và nhiệt độ chất quang dẫn là 21°C.
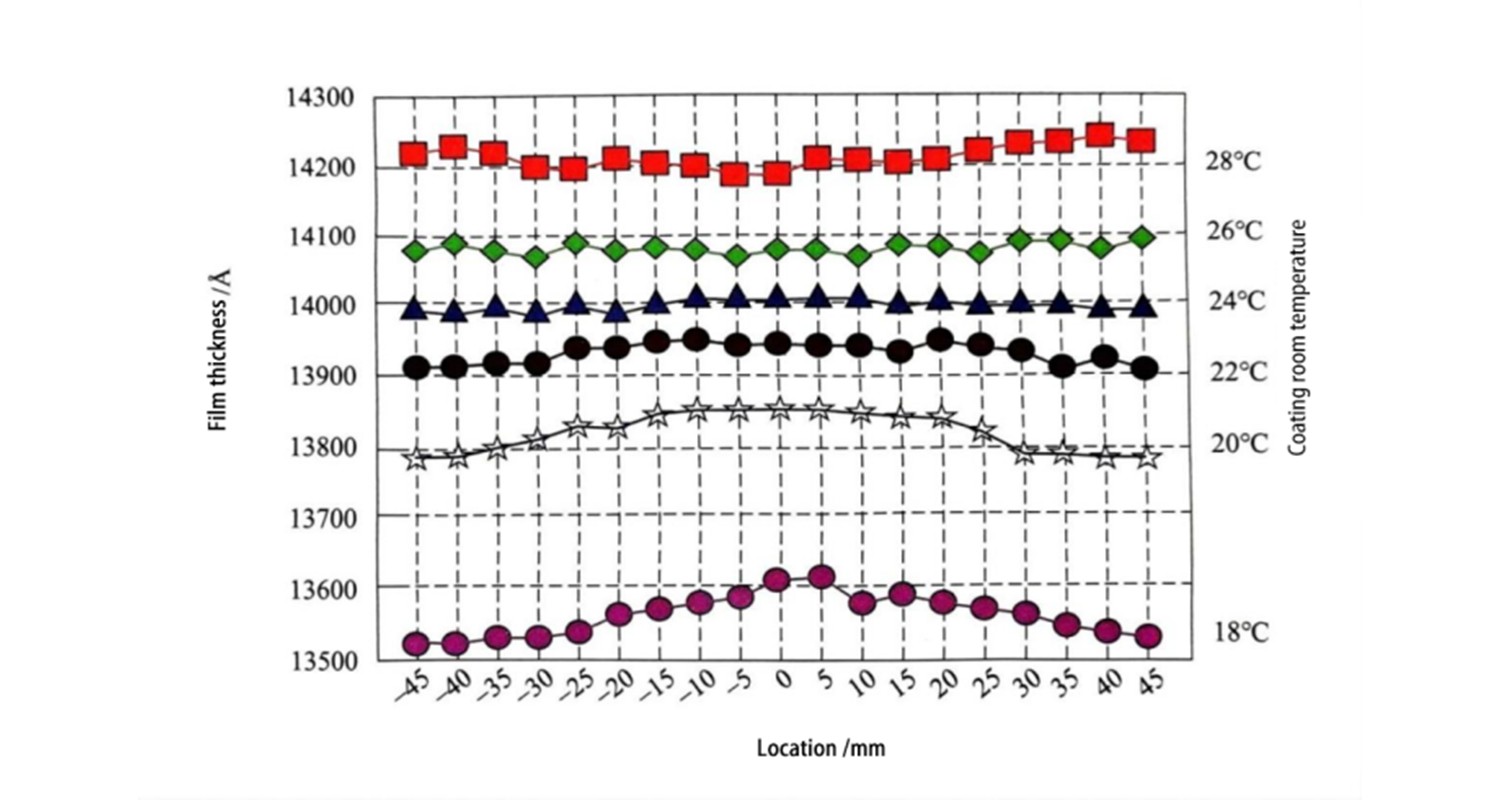
Hình 5: Mối quan hệ giữa nhiệt độ và phân bố độ dày màng sơn trong quá trình phủ
Ảnh hưởng của tốc độ thoát khí trong quá trình phủ
Hình 6 cho thấy mối quan hệ giữa tốc độ xả và phân bố độ dày màng. Trong trường hợp không có khí thải, chứng tỏ tâm của tấm wafer có xu hướng dày lên. Việc tăng tốc độ xả sẽ cải thiện độ đồng đều, nhưng nếu tăng quá nhiều thì độ đồng đều sẽ giảm. Có thể thấy rằng có một giá trị tối ưu cho tốc độ khí thải.
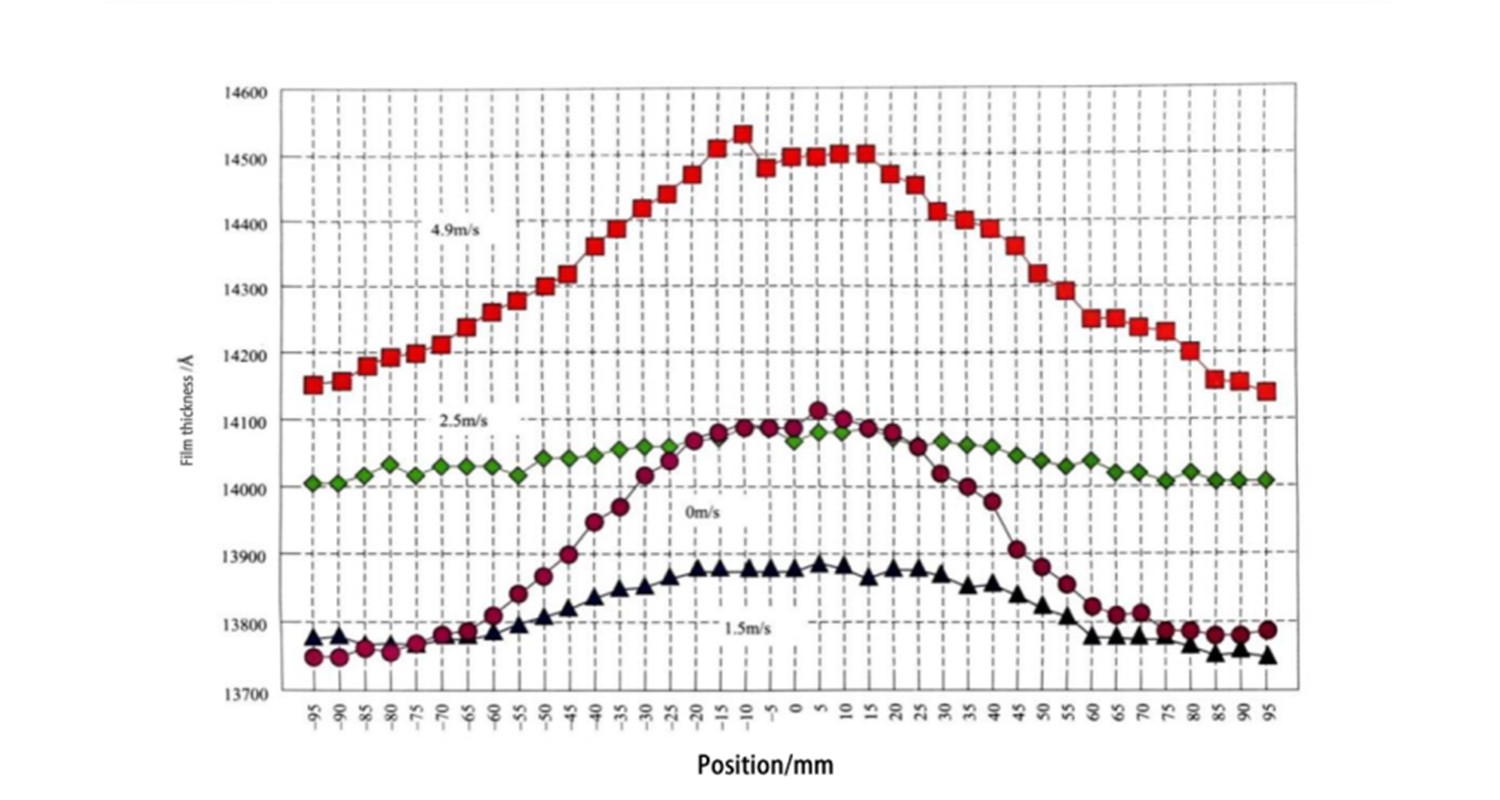
Hình 6: Mối quan hệ giữa tốc độ xả và phân bổ độ dày màng
điều trị HMDS
Để làm cho chất quang dẫn trở nên dễ phủ hơn, tấm bán dẫn cần được xử lý bằng hexamethyldisilazane (HMDS). Đặc biệt khi hơi ẩm bám vào bề mặt màng oxit Si sẽ hình thành silanol làm giảm độ bám dính của chất quang dẫn. Để loại bỏ độ ẩm và phân hủy silanol, tấm bán dẫn thường được làm nóng đến 100-120°C và phun sương HMDS để gây ra phản ứng hóa học. Cơ chế phản ứng được thể hiện trên Hình 7. Thông qua xử lý HMDS, bề mặt ưa nước có góc tiếp xúc nhỏ trở thành bề mặt kỵ nước có góc tiếp xúc lớn. Làm nóng wafer có thể thu được độ bám dính quang điện cao hơn.
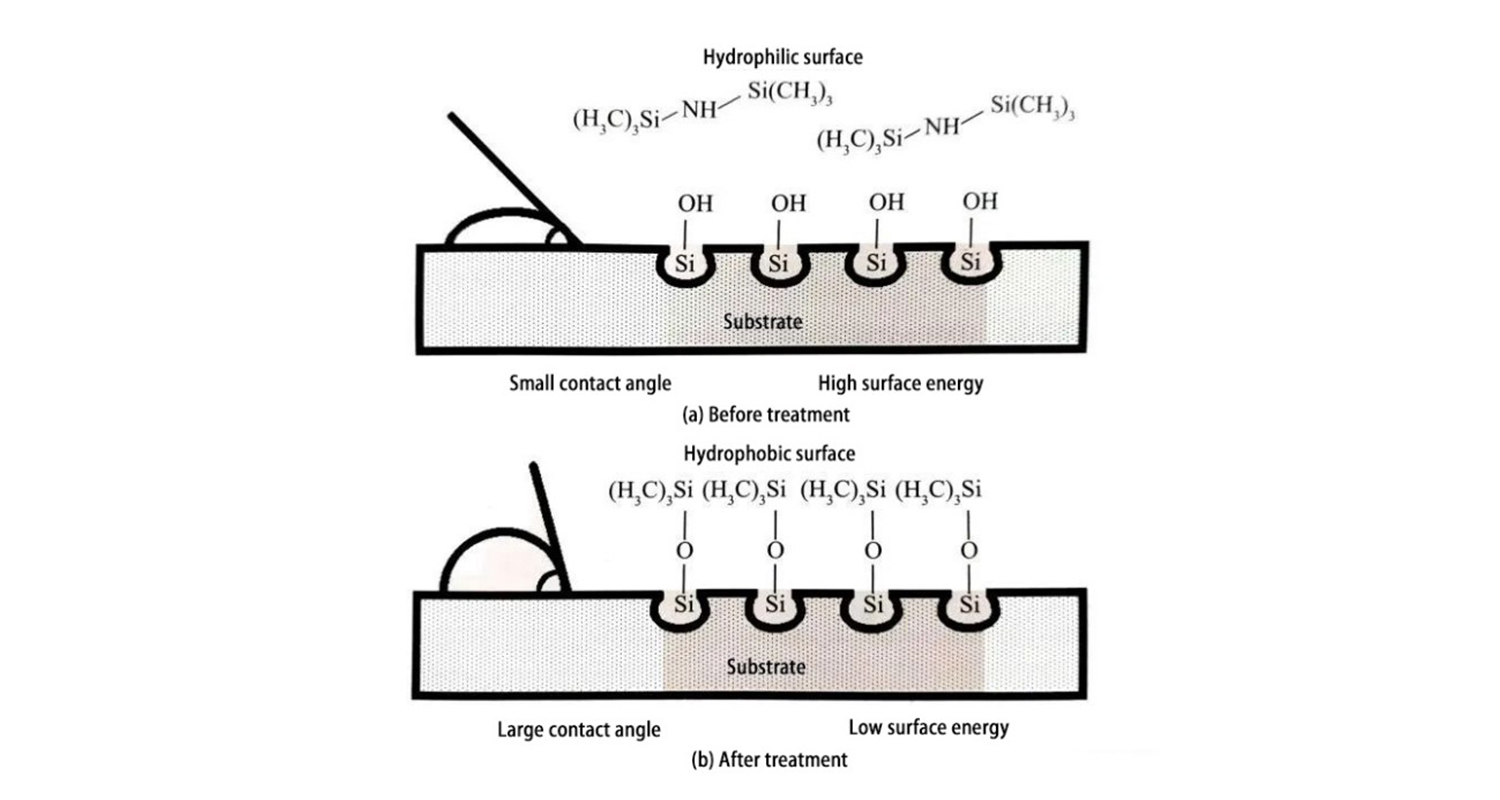
Hình 7: Cơ chế phản ứng HMDS
Hiệu quả của việc xử lý HMDS có thể được quan sát bằng cách đo góc tiếp xúc. Hình 8 thể hiện mối quan hệ giữa thời gian xử lý HMDS và góc tiếp xúc (nhiệt độ xử lý 110°C). Chất nền là Si, thời gian xử lý HMDS lớn hơn 1 phút, góc tiếp xúc lớn hơn 80 ° và hiệu quả xử lý ổn định. Hình 9 thể hiện mối quan hệ giữa nhiệt độ xử lý HMDS và góc tiếp xúc (thời gian xử lý 60 giây). Khi nhiệt độ vượt quá 120oC, góc tiếp xúc giảm, cho thấy HMDS bị phân hủy do nhiệt. Do đó, xử lý HMDS thường được thực hiện ở 100-110oC.
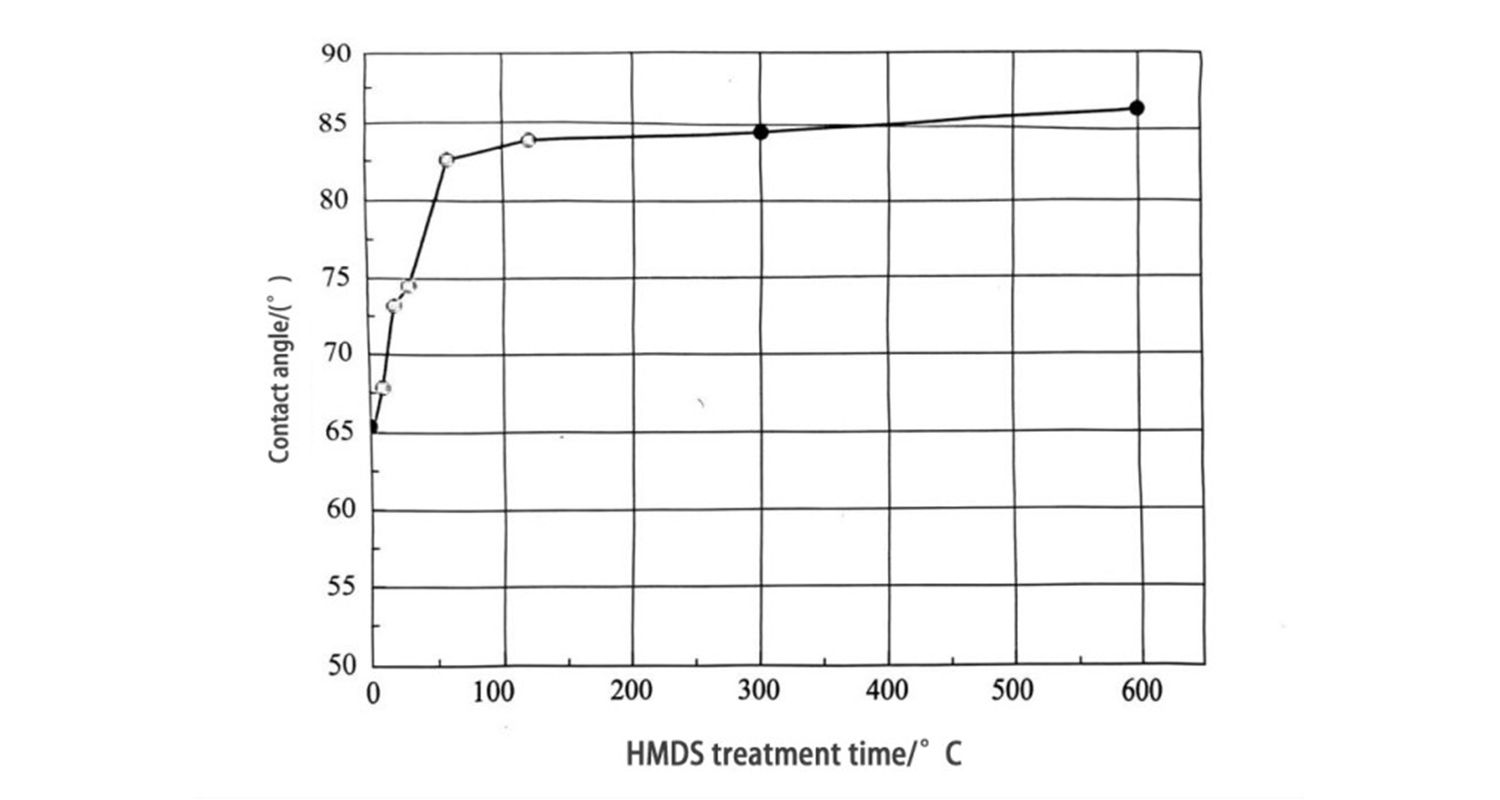
Hình 8: Mối liên quan giữa thời gian điều trị HMDS
và góc tiếp xúc (nhiệt độ xử lý 110oC)
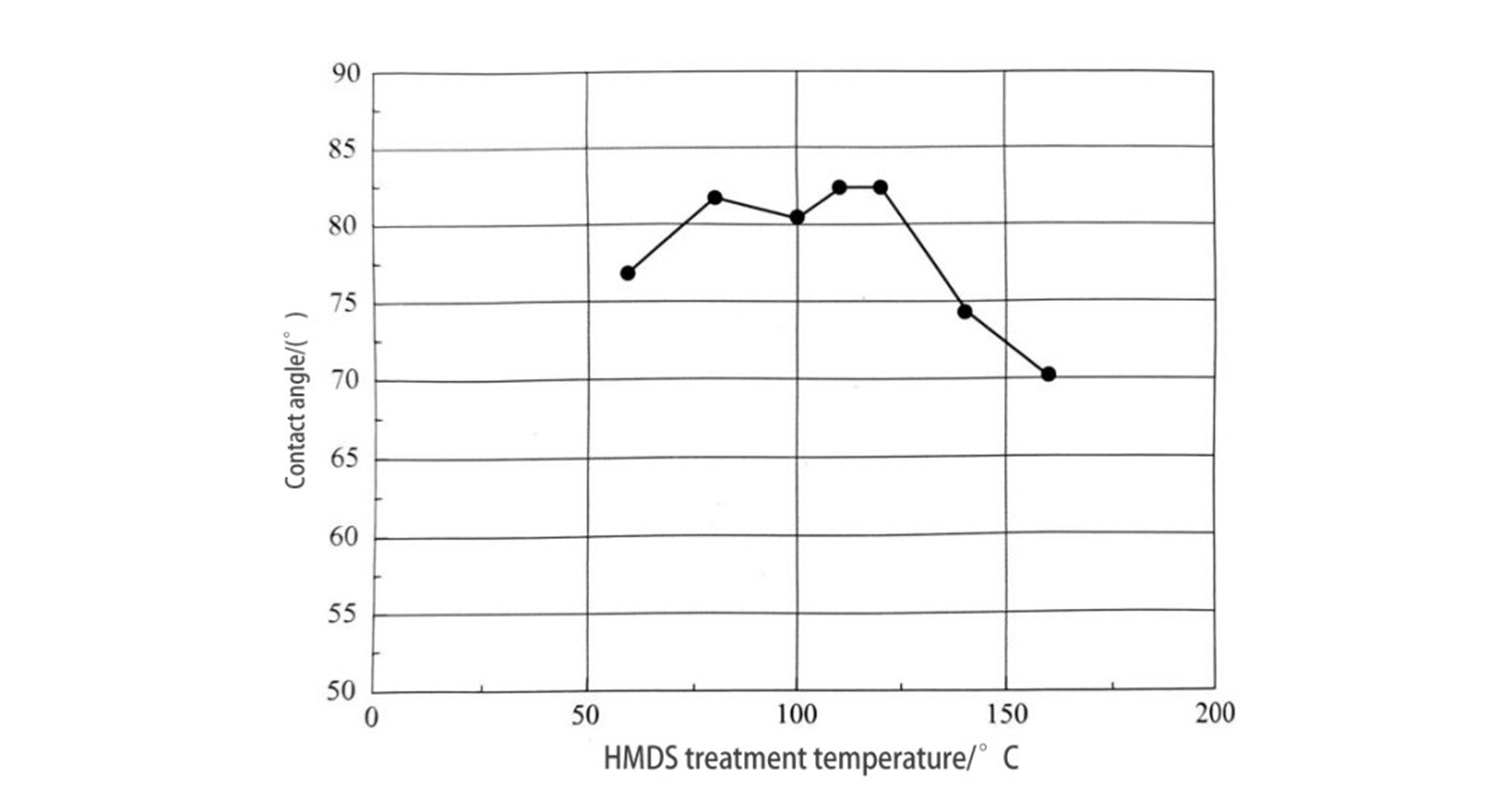
Hình 9: Mối quan hệ giữa nhiệt độ xử lý HMDS và góc tiếp xúc (thời gian xử lý 60s)
Việc xử lý HMDS được thực hiện trên đế silicon có màng oxit để tạo thành mẫu quang điện. Sau đó, màng oxit được khắc bằng axit hydrofluoric có thêm chất đệm và người ta thấy rằng sau khi xử lý HMDS, mẫu chất cản quang có thể được giữ không bị bong ra. Hình 10 cho thấy hiệu quả của việc xử lý HMDS (kích thước mẫu là 1um).
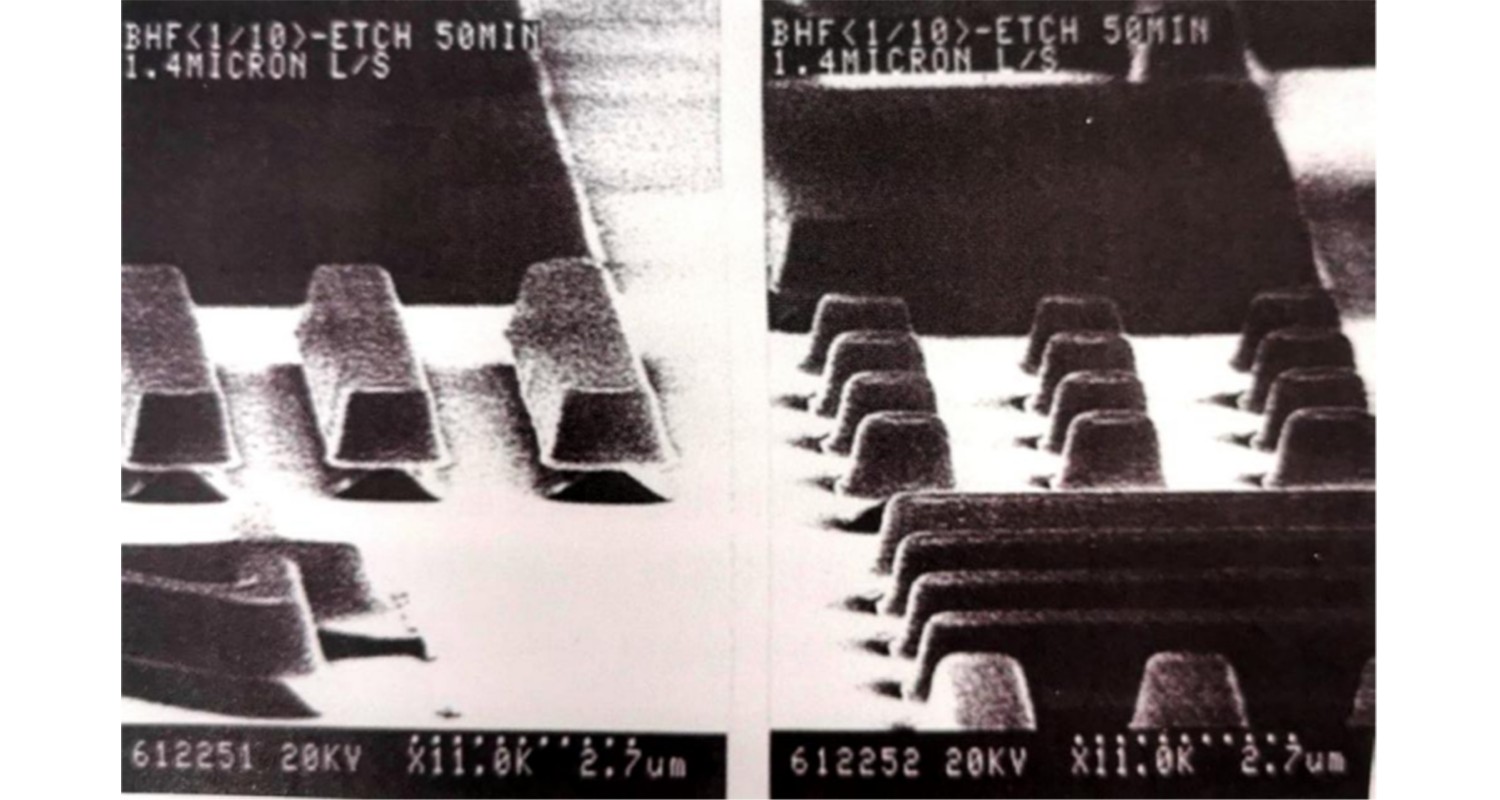
Hình 10: Hiệu quả xử lý HMDS (kích thước mẫu là 1um)
Nướng trước
Ở cùng tốc độ quay, nhiệt độ nung trước càng cao thì độ dày màng càng nhỏ, điều này cho thấy nhiệt độ nung trước càng cao thì dung môi bay hơi càng nhiều, dẫn đến độ dày màng mỏng hơn. Hình 11 thể hiện mối quan hệ giữa nhiệt độ trước khi nướng và thông số A của Dill. Thông số A biểu thị nồng độ của chất cảm quang. Như có thể thấy trên hình, khi nhiệt độ trước khi nướng tăng lên trên 140°C, thông số A giảm, cho thấy chất cảm quang bị phân hủy ở nhiệt độ cao hơn nhiệt độ này. Hình 12 cho thấy độ truyền quang phổ ở các nhiệt độ trước khi nướng khác nhau. Ở 160°C và 180°C, có thể quan sát thấy sự gia tăng độ truyền qua trong phạm vi bước sóng 300-500nm. Điều này khẳng định chất cảm quang đã được nung và phân hủy ở nhiệt độ cao. Nhiệt độ trước khi nướng có giá trị tối ưu, được xác định bởi đặc tính ánh sáng và độ nhạy.
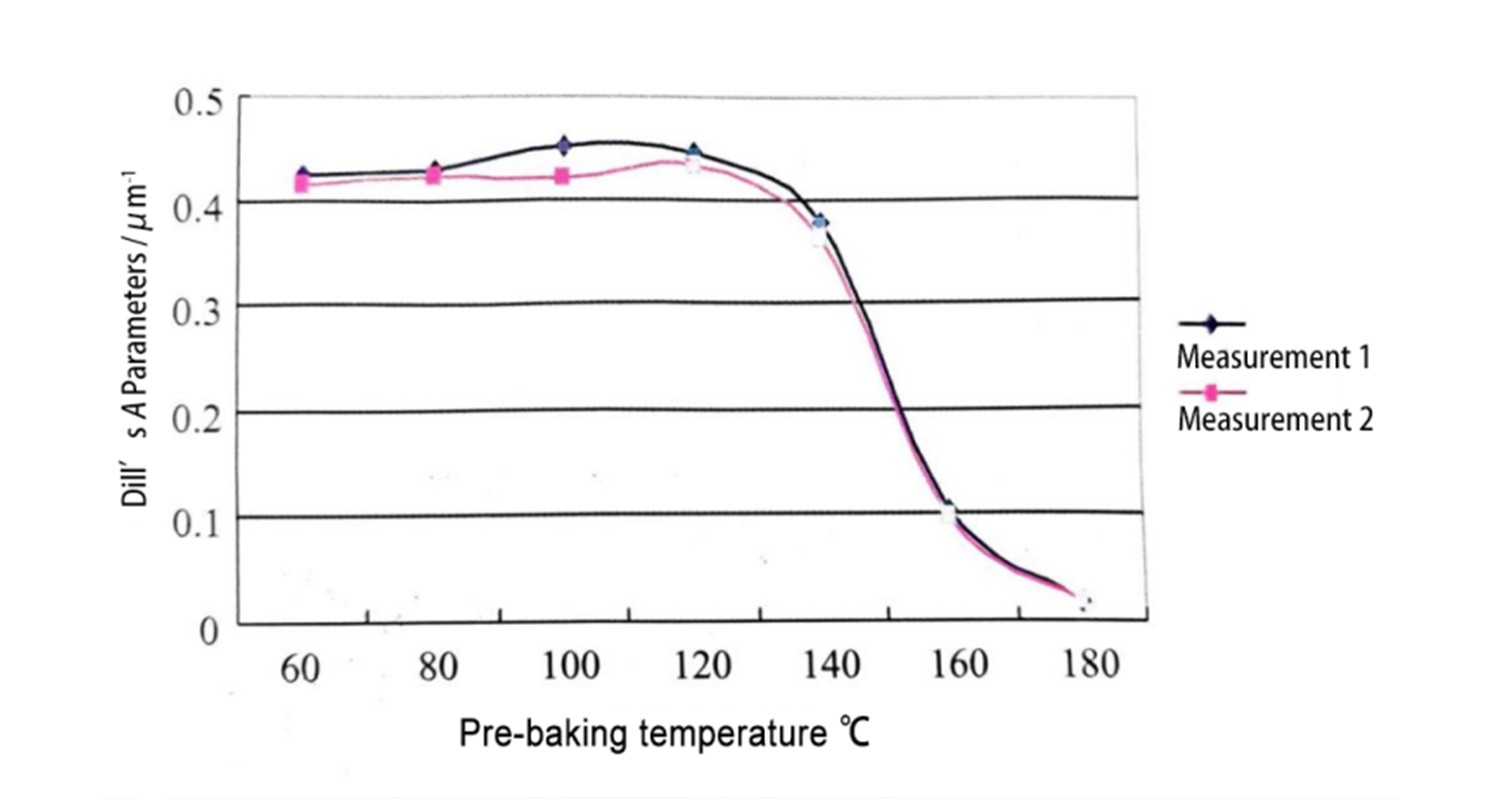
Hình 11: Mối quan hệ giữa nhiệt độ trước khi nướng và thông số Dill's A
(giá trị đo của OFPR-800/2)
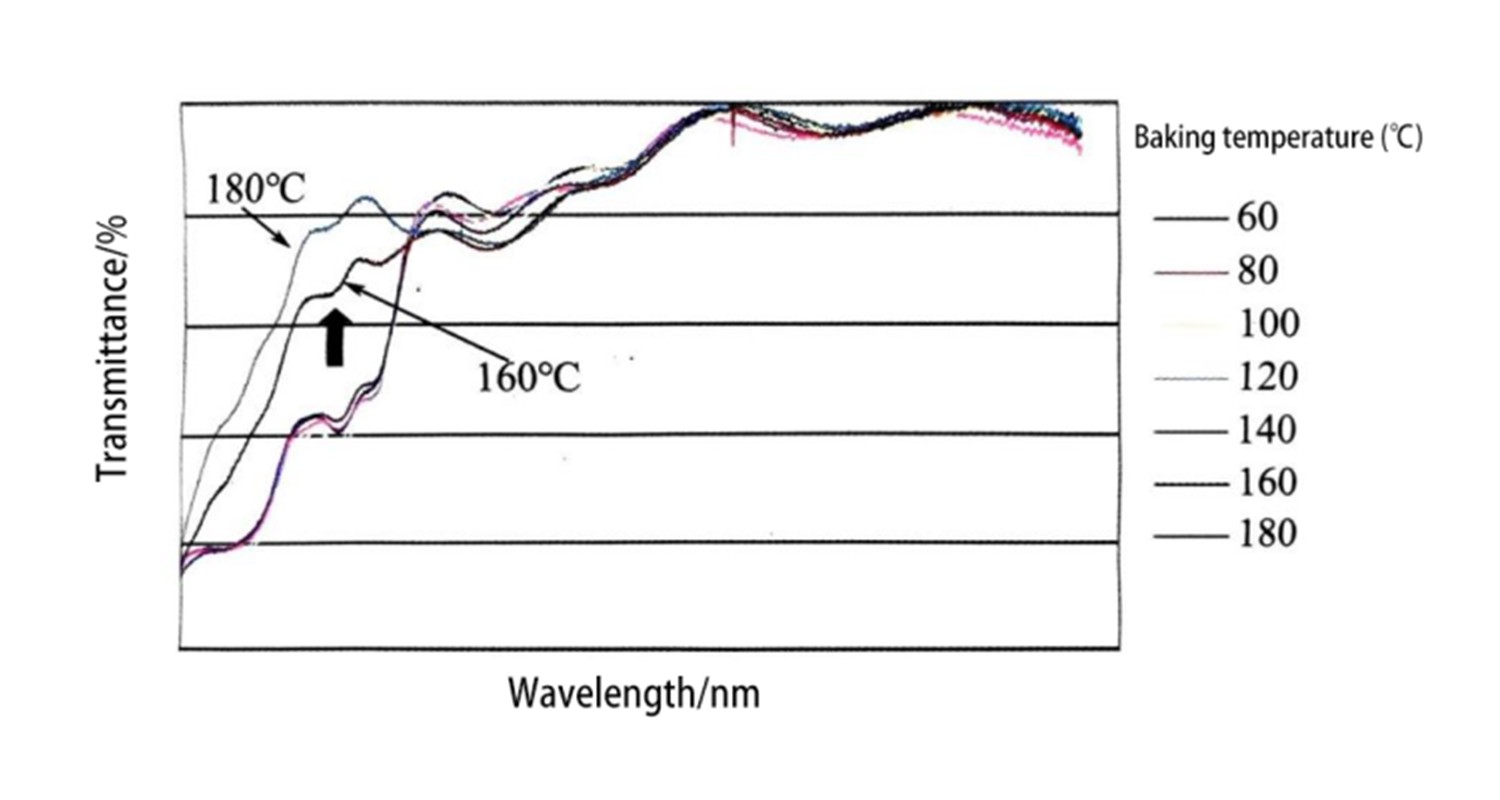
Hình 12: Độ truyền quang phổ ở các nhiệt độ trước khi nướng khác nhau
(OFPR-800, độ dày màng 1um)
Nói tóm lại, phương pháp phủ quay có những ưu điểm độc đáo như kiểm soát chính xác độ dày màng, hiệu suất chi phí cao, điều kiện quy trình nhẹ và vận hành đơn giản nên có tác dụng đáng kể trong việc giảm ô nhiễm, tiết kiệm năng lượng và cải thiện hiệu suất chi phí. Trong những năm gần đây, lớp phủ kéo sợi ngày càng được chú ý và ứng dụng của nó dần lan rộng sang nhiều lĩnh vực khác nhau.
Thời gian đăng: 27-11-2024